Contributed by Yasuoki Takeuchi, President, Razor Club
The steel strip used to make the razors we shave with every day has a surprisingly close connection to the famous Japanese swords and razors of the world. It is a little-known fact, but if we look at the origin of the famous sword Masamune, the swordsmiths of the time used iron sand from the San’in region of Shimane Prefecture for the tama-hagane (tama-hagane) used in the blade, and used the high-purity steel made by the tatara process, an ancient Japanese iron-making technique, to make the sword with their skillful techniques. The iron sand itself is a local flower. Iron sand itself is contained in granite in this area, and 1% of it is iron sand. In the past, iron sand precipitated in the river was scooped up by humans using a colander. This method was called the specific gravity beneficiation method, and this style of mining is said to have become the “Dojosukui” of the Yasugi-bushi (traditional Japanese ballad). According to the story, the iron sand was originally extracted from the soil, but it was misheard by performers in Edo (present-day Tokyo) and the name “dojosukui” came to be used. Nowadays, a magnetic ore dressing method using a magnet and a machine is adopted. Thus, the traditional “Tatara method of making tama-hagane” is now mass-produced as material for razors (steel strips) under a different manufacturing method. High-grade steel made from iron sand refined by the “Yasugi method” from iron sand with few impurities is called YSS YASUKI HAGANE, which is also used as material for razors (steel strip).

Iron Sand Sand in Granite, Yasugi, Shimane Prefecture, Japan, Hitachi Metals, Ltd.
Author, April 23, 1985

The “tatara” iron-making process, an ancient iron-making technique, is carried out for about 70 hours over three days and nights from the time the fire is turned on to the time the air supply is stopped.
Torigami Mokuzan Ironworks in Yokota-cho, Shimane Prefecture, April 23, 1985.
https://www.hitachi-metals.co.jp/tatara/index.htm
As time passed and the demand for razors grew in today’s highly consumer-oriented society, the consumption of steel strip increased rapidly. Among them, razor manufacturers such as Gillette, Schick, and ASR in the U.S., Malhotra in India, and Wilkinson in the U.K. use a large portion of this steel. It is also clear that the consumption of razors is growing in Western countries and other developed countries. The material used in once famous swords is now being substituted for razor blades, and Japanese blade steel is now recognized by razor manufacturers around the world, with Hitachi Yaski-Hagane now supplying approximately 65% of all shipments to razor manufacturers worldwide. Next in line are Sweden’s Sandvik and Britain’s Brite Steel, but the gap between the two companies shows no sign of narrowing. Steel products produced in Japan are exported to the rest of the world, and many Japanese are using them as finished products (Schick, Gillette, etc.). Since the end of World War II, while domestic products such as automobiles and home appliances have surpassed foreign products, only wet razors have been overwhelmed by American products, with a market share of more than 60%. This situation is a rare example of the trade structure of our country!
I once asked a person directly involved in this field why Japanese yasuki hagane has become so popular. The answer is that the reason is the reliable homogeneity and stable supply, as well as the superior service. In the past (1960s), Hitachi Metals had also commissioned a razor manufacturer in Seki City, Gifu Prefecture, to market a replacement blade under the trade name Sunblade, but eventually backed out of the business. However, the company eventually withdrew from the market. This was because of unexpected problems that a materials manufacturer could not anticipate. After that, the company made a fresh start as a materials manufacturer and began doing business with Gillette when it established a branch office in the United States. The efforts of Kenji Takitani (former vice president of Hitachi Metals, Ltd.), who looks back on those days, have improved the quality of the products from razor blades to the parts used in many sophisticated semiconductors. The demand for high-grade specialty steel, derived from razor blades, has expanded its applications in today’s advanced information society, and in the midst of today’s steel industry seeking global expansion through M&A and other means, Hitachi Metals has focused on niche markets and spent years building its own presence and superiority. No other manufacturer can match the corporate strategy of Hitachi Metals, Ltd. This is the reality today.
The 1960s and 1970s were a period of economic recovery in Japan. During this period, the retail industry saw a major shift in consumption patterns as well as distribution innovations, with Mitsukoshi Department Store giving up its dominant position in terms of sales to Daiei, a mass merchandiser. Meanwhile, Japan’s exports were also gaining momentum, and many companies in the automobile and consumer electronics industries were heading to overseas markets to earn foreign currency. The samurai spirit of Japan came together to save their country after the war and laid the foundation for Japan to become an economic superpower. Hitachi Metals was no exception. In December 1963, under the leadership of then President Ryuichi Nakamura, a 37-year-old employee began a sales pitch to Gillette, the largest razor manufacturer in the Boston area. The company continued to maintain a deep relationship of trust and worked hard to develop the best materials. In April 1971, he began doing business with Schick, and since then, he has been working with world-class razor manufacturers such as Wilkinson in the U.K., ASR in the U.S., and Malhotra in India. At the age of 36, he went to the U.S. on his own to open a branch office, and his achievements during his 11 years in the U.S. were remarkable. When he returned to Japan on June 21, 1974, he bid farewell to 700 people, including employees of local subsidiaries. When he returned to Japan on June 21, 1974, he bid farewell to 700 people, including employees of local subsidiaries. This is a romantic story of a man and an emotional drama at the same time. He is one of the key figures who played a role in making Japan the trading powerhouse that it is today. In my conversations with him, he always says firmly, “This is a success story that I could not have achieved on my own, thanks to the high quality materials. He is a genuine Hitachi Metals man, a graduate of Tokyo University and a Fulbright recipient in the second year of his Fulbright program. I have known Mr. Kenji Takitani for more than 30 years and have learned a great deal from him. I am honored to have known him for more than 30 years.

June 1972
Hitachi Metals U.S. Headquarters Established in Suburban New York
Kenji Takitani, 46, at the opening party
By the way, the manufacturing process of razor blades does not vary greatly among manufacturers. However, the manufacturing process from the steel strip (die-cutting, quenching, tempering, blading, and coating) to the production method, including the material of each material, is strictly different from company to company. This is the characteristic of each company, and it has also become a patent right. To cite a few examples by year, a stainless steel replacement blade in 1956, a blade made in 196, a blade made in 1967, and a blade made in 1973. The first was a stainless steel blade in 1956, the second was a coating on the blade edge in 1961, and the third was a three-layer ceramic coating in 1974, all from Wilkinson in the U.K., and the third was a two-layer coating in 1972. The two blades from 1972 and the lubricant on the skin (Lublasturip) from 1986 are from the U.S. company Gillette. The first razor with a guard was sold by Feathers in Japan in 1994, and the following year, the first razor with a guard was sold by Feathers in the U.S.A. The following year, the well-known protector with the advertisement, “It won’t cut! In the last decade, three-blade, four-blade, and five-blade razors were launched one after another, with Japan’s Kaijirushi and the U.S.-based Chic and Gillette leading the way. In the intervening period, the transition from two blades to five blades took only 35 short years. Naturally, products have become increasingly high-end and multifunctional with added value and safety, but at the same time, prices have increased many times over. Accordingly, development costs have also increased dramatically compared to the single-blade and double-blade eras. This trend is a strategic milestone for manufacturers, and is reflected in improved business performance.

September 29, 1989
Received a commemorative cup of appreciation from Coleman M. Mockler, Jr, Chairman (CEO) at Gillette’s headquarters in Boston, U.S.A.
Finally, Mr. Yoshihiro Honda, who has been in charge of razor materials for many years and has been very active in this field and is nicknamed “Mr. Razor” among razor manufacturers, is an excellent expert in the manufacturing technology of steel strip. He has also made a great contribution to the spread of YSS Hitachi YASUKI HAGANE, which now holds 65% of the world market share, through his presence and hardships. In 2000, he was promoted to president of the head office, and in 2006, he became chairman of the board. He must also be praised by many of his shareholders for his achievements during the turbulent six years between 2000 when he was promoted to president of the head office and 2006 when he became chairman of the board. The razor is here as a finished product on the side. What will people feel when they see it, pick it up, and use it? How will they evaluate the value of this razor? In fact, I have seen many material makers and razor makers working earnestly toward technological innovation. It is truly a composition of cooperation born of trust, where good materials produce good products. And the meaning and weight of my father’s words, “Good products have no borders,” which he used to say during the razor liberalization era in the 1960s, still ring true in my mind. The meaning and weight of these words come to mind. Coincidentally, during that period, the yen appreciated from ¥360 to ¥115 against the U.S. dollar. I believe that this must have been a major factor that accelerated the internationalization of the razor market.

July 16, 1993
At Yasugi Works, Shimane Prefecture, Hitachi Metals, Ltd. From left: The author, his father Kinzo Takeuchi, Yoshihiro Honda (then Yasugi Works General Manager), and Kenji Takitani (former Vice President of Hitachi Metals).

July 21, 2000
Center: then President Yoshihiro Honda, Left: The author, Right: Noriki Takeuchi (Razor Club) at the President’s Office, Hitachi Metals, Ltd.
For the first time in about 15 years, I visited Hitachi Metals’ Yasugi Works near Yonago Airport in Shimane Prefecture. The former president and current chairman of the company, Mr. Yoshihiro Honda, with whom I have had a business relationship for 30 years, kindly allowed me to visit the Yasugi Works for the first time to see the integrated production process of high-grade Yaski-hagane including steel strip, which is used for razors and blades, mainly by his son’s generation. I had the opportunity to see and learn about the integrated production process of high-grade YASUKI HAGANE, including the steel strip used to make razors and blades, mainly from his son’s generation. Especially in the field of razor blade replacement, the supply rate of steel strip, including Gillette, Chic, Wilkinson, ASR, and other overseas razor manufacturers, as well as domestic companies such as Feather and Kaijirushi, far exceeds that of BS in England and SB in Sweden, and has reached 70% of the global market. The company’s supply rate of steel strips has reached 70% of the world market, far exceeding that of BS in the U.K. and SB in Sweden. The display case in the factory had already displayed many razors with three, four, and five blades, which made me realize how the times have changed since I arrived 15 years ago, when the world was enjoying the two-blade era. The story of the company’s history is that it was spun off from Hitachi, Ltd. in 1956 and changed its name to Hitachi, Ltd. in 1967. In 1967, the company name was changed to Hitachi Metals, Ltd. The company has six plants scattered across Japan, but the Yasugi Works of the Special Steel Company is the largest, boasting a total site area of approximately 280,000 tsubo (approximately 1.2 million square meters), including the Kaigan Works and the Yamate Works. The main building, a wooden structure formerly located at the Yamate Works, has been relocated to the Kaigan Works site and has been replaced by a modern building. On the other hand, Kinyako Shrine, the ancestral god of iron and steel, stands on a hill within the grounds of the Yamate Plant. Below, several factory buildings can be seen in a row. Nearby is the Wako Museum, which tells the story of the world and history of Japanese steel, including tama-hagane (tamahagane), which was produced using tatara iron manufacturing methods, and old swords. The director of the museum, Yasumuneo Yaso, is also a doctor of engineering and worked as an engineer at the Yasugi Works of Hitachi Metals. I remember a well-informed person who said in a newspaper, “Steel is the nation, and steel is the rice of industry. In Japan, the annual production of crude steel, which is used in large quantities for automobiles and buildings, amounts to more than 120 million tons, but the production of specialty steel, such as razor steel and high-quality materials used in information equipment, is low by comparison.
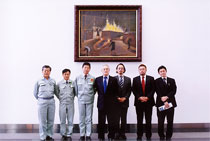
October 7, 2008
Visit to Yasugi Works, Shimane Prefecture, Hitachi Metals, Ltd.
Observing the manufacture of razor materials and other steel strip products.
In the center is Yasuoki Takeuchi, and next to him on the left is Plant Manager Murayama.